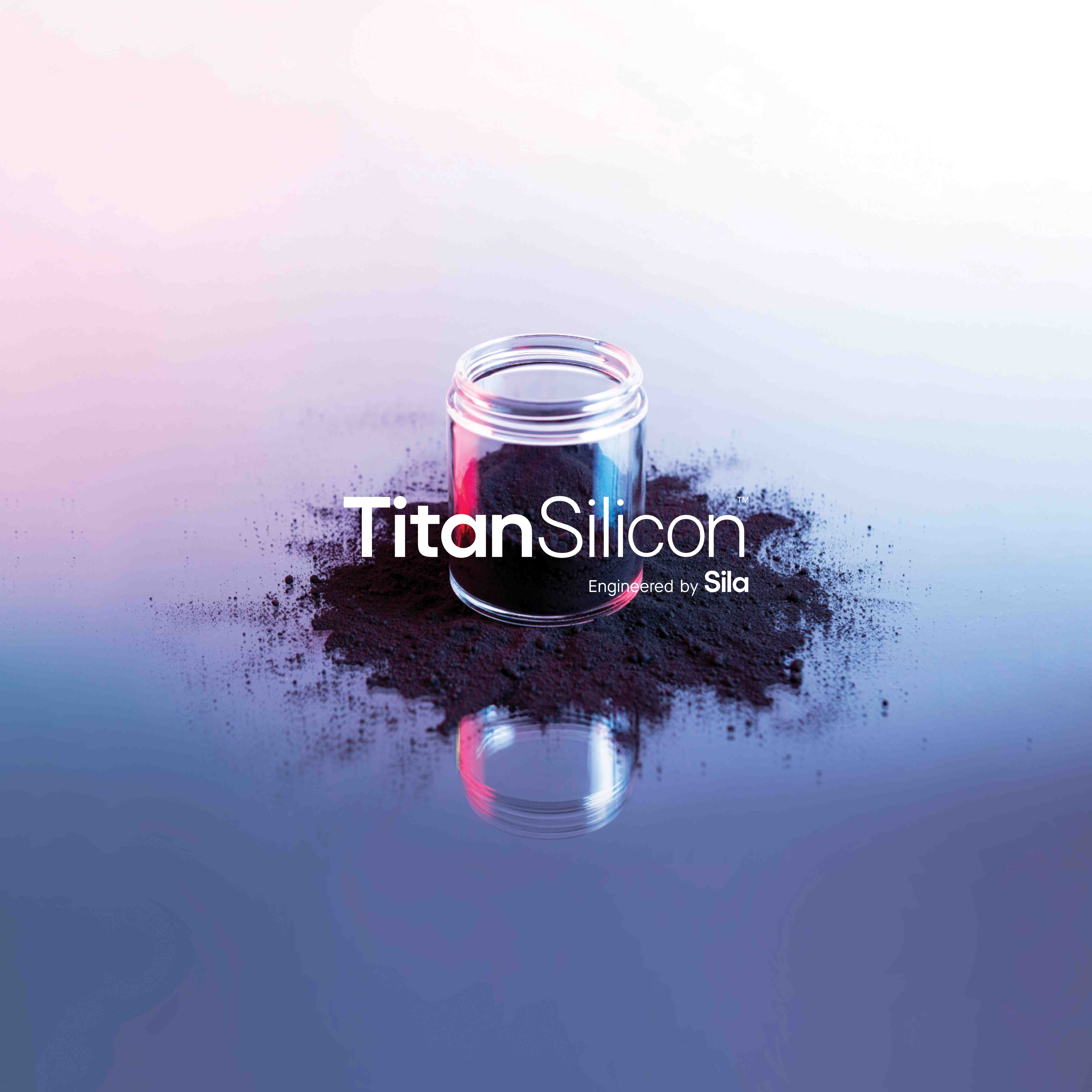
The high energy density battery from Panasonic using Titan Silicon is expected to enable automakers to deliver unmatched EV performance, dramatically increasing vehicle range and reducing charge times. Sila’s anode materials, to be produced in the company’s plant in Moses Lake, WA, will be optimised for Panasonic’s next-generation lithium-ion batteries.
Panasonic Energy is recognised as a global leader in advancing performance, innovation, and production of automotive batteries. To meet the rapidly growing demand for EVs, the company plans to increase global production capacity of automotive batteries to 200 GWh by 2030. The company has also announced its commitment to developing pioneering performance battery technology, by delivering increased volumetric energy density to 1,000 Wh/L by FY30/31. By partnering with Sila to optimise the proven performance gains already achieved with Titan Silicon, Panasonic Energy will be able to take a major step toward achieving its goal of 1,000 Wh/L.
“By integrating Sila's groundbreaking battery material with our advanced cell manufacturing capabilities, we believe that we can address the concerns such as range anxiety and charging time and contribute to accelerating the adoption of EVs,” said Shoichiro Watanabe, executive VP of Panasonic Energy.
Sila was the first to bring next-generation anode materials to market with the launch of Titan Silicon in the Whoop 4.0 in 2021. In 2022, the company was the first next-generation battery materials company to sign a supply agreement with a global auto manufacturer, Mercedes Benz. And now, Sila partners with the world’s leading cell manufacturer to redefine what’s possible for EV range and charge times.
Sila’s Titan Silicon is the first market-proven graphite anode replacement, engineered for mass scale and high performance, delivering a 20% increase in range today, with a development runway to double those gains. Sila’s nano-composite silicon also improves battery charging time with the aim to drive charge times down to a mere ten minutes. Titan Silicon generates substantially less CO2 per kWh than graphite during production and is US manufactured, enabling automakers to meet requirements for the Inflation Reduction Act tax credits.